Atlas Copco air compressors are leaders in the global supply of compressed air and gas equipment. In addition, Atlas Copco are known as industry-leading suppliers of quality generators in addition to industrial tools.
Their compressors and vacuum pumps are used in numerous end markets, such as automotive assembly and food processing.
With a strong balance sheet and low debt to EBITDA ratio, they can bring numerous solutions to markets worldwide.
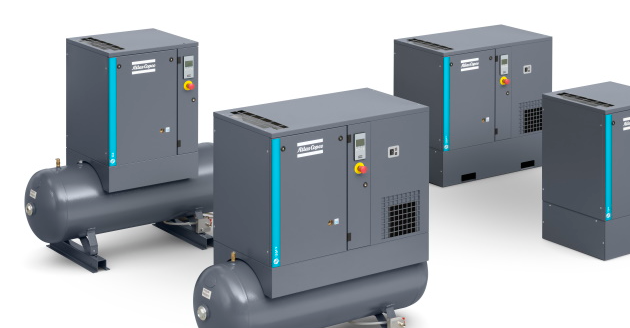
How Air Compressors Work
Air compressors utilise air to propel a variety of tools. Additionally, they pump, inflate, and break down materials.
They can also be employed to eliminate debris or puddles of water from a yard.
These compressors come in single phase or dual phase configurations. Single phase units are ideal for residential settings, while dual phase is ideal for industrial uses like vehicle repair shops and presses
Air compressors are essential machines that supply air to tools and other pneumatic devices in factories and workshops around the globe. Although they’re relatively recent innovations compared to machine age history, air compressors have revolutionised how we work with tools and air. Before air compressors, most tools relied on large systems including wheels, belts and other components – often large, bulky and costly for small businesses to afford.
Modern air compressors are user-friendly and come in a range of sizes and shapes. Additionally, they’re portable, quiet, and durable – making them ideal for DIY projects or small businesses.
An air compressor’s main element is a pump that transforms electric energy into pressurised air. This compressed air can then be used for driving various pneumatic tools like nailers and impact wrenches.
In addition to an air pump, an air compressor also includes a regulator which adjusts the pressure of compressed air. This regulator is essential in all air compressors since it allows users to regulate both volume and quality of compressed air.
Most air compressors work by compressing air in multiple steps. Each stage involves a distinct process and produces different air flow rates. CFM, or cubic feet per minute (CFM), is the industry standard for measuring compressor output – the volume of compressed air produced.
For instance, a compressor with a higher CFM value can produce more air per minute than one with a lower one. This makes the compressor more efficient, leading to savings in electricity and energy costs over time.
To reduce friction, some air compressors incorporate lubricant into their compression chambers. However, this isn’t mandatory for all compressors; some types don’t use oil at all.
Air compressors come in four main formats, each featuring its own specific air displacement mechanism: scroll, rotary screw, rotary vane and reciprocating piston. The first three are positive displacement units which compress air by using one compression cylinder to draw in atmospheric air and reduce its volume before storing it for later use.
Atlas Copco is the undisputed leader in oil-free compressed air, dedicated to providing clean and contamination-free compressed air for food and beverage industries. Atlas Copco air compressors are engineered for efficiency without lubrication, so they can withstand even the toughest conditions that this industry demands.
The Advantages of Air Compressors
Air compressors are a highly useful piece of equipment that can be employed for many tasks. Not only are they easy to operate and maintain, but their strength and longevity also speak for themselves.
They are a popular choice for manufacturing industries as they produce oil-free compressed air for pneumatic tools. Furthermore, their capabilities extend to operating at extreme temperatures and in places where other forms of energy may not be permitted due to explosion or fire hazards.
Energy Efficiency
Energy efficiency is one of the primary advantages of air compressors. It can reduce system energy requirements by as much as 20%, potentially saving thousands in energy costs over its lifespan.
Energy prices continue to rise, leading facility managers across a wide range of industries to seek ways to reduce their operational expenses. This could involve saving money on electricity while maximising uptime and improving production rates.
Compressors are a major source of energy consumption in many industrial facilities. They take in air at one pressure and release it at higher pressure to drive equipment such as manufacturing robots, pneumatic tools, paint sprayers and more – accounting for six per cent of all motor-driven electricity consumed within this sector.
These new standards include specific power requirements and testing methods that manufacturers must meet. Companies must certify their compressors meet these specifications.
To certify a compressor meets the new energy efficiency standards, manufacturers must have it tested according to DOE’s test procedure and maintain records of results for 10 years. These records will then be accessible to the public during that time.
Though new standards have yet to be set, many compressor manufacturers have already started making energy efficiency improvements. In countries like Europe or the European Union with stricter laws, government-sponsored rebate programs may help spur sales of energy-saving compressors.
Less Noise
Air compressors are indispensable tools for many tasks, from powering pneumatic tools to inflating tires, rafts and sports balls. But their noisy operation can be a distraction to both the operator and others nearby.
Good news! There are several methods available to reduce noise from an air compressor. These include sound insulation, vibration dampening and maintenance practices.
One simple way to reduce the sound of your air compressor is by installing an intake silencer. This can reduce overall noise up to 2 to 4 dB, making it ideal for larger models that have oiled filters or continuously running features.
Another way to make your compressor quieter is by placing it in a room with good acoustics. This will muffle any noises coming from the compressor and prevent them from being reflected off walls or ceiling.
Soundproofing a room can be achieved using acoustic panels or foamboard, which come in various colours and materials. When combined with sound blankets, these materials further minimise noise from compressor noises.
You could also cover the unit with acoustic curtains, which can be purchased from most hardware stores and easily installed over the machine.
If you work in an industrial setting or workshop, controlling the noise from your compressor is paramount to ensure safe and productive work. A loud compressor can be hazardous for workers without proper hearing protection, and it also slows down team productivity.
To reduce noise levels from an air compressor, select one designed for quieter operation. Many factors contribute to decibel output of an air compressor such as type, pump design and material of components.
Entry-level single-piston pumps tend to be quite loud, but similar compressors made from higher-quality materials will create less noise. Rotary screw compressors, which use two helical screws instead of a reciprocating piston motor, are much quieter since they don’t come into direct contact with each other.
Less Wear and Tear
Air compressors are indispensable tools for many. They power pneumatic tools, lay down an even coat of paint and more; thus, it is essential that they be maintained correctly. In order to reduce the number of maintenance issues that occur, regular inspections and checkups should be performed.
Compressors that are used frequently require lubrication to protect them against wear and tear, making them cost-effective to run in the long run.
Quality lubricant can be purchased at most hardware stores or online. Opt for one with a high synthetic content for maximum protection against moisture buildup from the environment, which could lead to rust within your system.
Utilising a higher-grade lubricant can help reduce friction between moving parts, increasing the lifespan of your compressor. Furthermore, this will make your machine more efficient.
Maintain the ideal operating temperature for your compressor. Ideally, this should be between 50 and 85 degrees F. This range allows the machine to run without freezing or overheating which could cause damage and malfunctioning.
Maintaining an ideal air temperature can extend the life of your air compressor by reducing heat production. It also improves indoor air quality by cooling air as it passes through its pipes and hoses.
Another way to extend the life of your compressor is to avoid short cycling. By repeatedly turning on and off, you are adding additional stress and strain on its motor, reducing its lifespan and raising operational expenses.
Maintaining the appropriate air temperature and avoiding frequent short cycling will significantly reduce wear and tear on your industrial air compressor. To do this, establish a comprehensive maintenance program that includes both regular oil changes and preventative upkeep.
Some simple tasks that can extend the life of your compressor include cleaning the inlet filter and replacing filters as necessary, performing leak checks and clearing dirt from its housing. Doing these small things can increase its lifespan up to 70%.
Less Maintenance
Air compressors are essential components of any industrial setting, and keeping them running optimally will save you money and extend the life of your equipment. While many companies rely on reactive maintenance plans that require service or repairs when problems arise, there are ways to maintain your compressor’s health and keep it functioning at full capacity.
Before anything else, create a maintenance budget and budget accordingly. Doing this will enable you to plan for routine work on your air compressor and prevent issues like broken filters or damaged belts from becoming major headaches in the long run.
Another way to guarantee your air compressor runs optimally is to keep it clean and lubricated. This can be accomplished using various techniques, such as routinely cleaning and changing filters.
Maintaining your air compressor regularly can reduce the risk of fires, electrical shorts and other safety incidents. Doing so helps you reduce potential injuries to employees.
Maintaining your air compressor properly can enhance productivity and efficiency at your facility, saving both time and money as you complete more projects faster.
Preventative maintenance also helps you stay ahead of any potential issues so that you don’t end up facing unexpected repair fees or downtime.
For instance, leaks can consume 20-30% of the energy your compressor uses. To save this cost, regularly inspecting and fixing leaks in your air system is a cost-effective way to ensure optimal efficiency.
Maintain the cleanliness and grease-free condition of your air hoses to avoid damage to their connection and diminished quality of air you receive. Furthermore, increase uptime by making sure your compressor has a large tank capacity so you don’t have to constantly refill it.
By following these straightforward steps, you can make your air compressor run more efficiently and safely while cutting the costs of maintenance. Furthermore, this will enhance your workplace environment by allowing for less noise and vibration during operations.
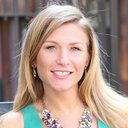
Olivia Harper is a writer passionate about exploring the latest developments in technology and digital solutions. She focuses on providing in-depth analysis, tech reviews, and news updates that keep readers informed and ahead of the curve.